
New lining technology upgrades Olympic Dam flash furnace
This lump-sum R5, 5-million contract was awarded to Bateman Engineering as a result of the successful completion of a similar cooling-system upgrade on the slag-cleaning furnace at Olympic Dam in...

Minerals Engineering International Online - Pyrometallurgy ...
The technology was employed in the design of new linings to upgrade two furnaces producing blister copper at Olympic Dam. In a below bath application, in late 2003, the sidewall lining of the electric-arc slag-cleaning furnace was replaced with CFMs because of the furnace’s short campaign life, which averaged around 13 months due to the severe stone corrosion of the refractory material.

Composite Furnace Module Cooling Systems in the Electric ...
Following successful trial work involving the installation of test Composite Furnace Modules in the sidewall of the copper slag-cleaning furnace at Olympic Dam, including an element that was ...

CiteSeerX — NOMENCLATURE
CiteSeerX - Document Details (Isaac Councill, Lee Giles, Pradeep Teregowda): During 2005 a safety issue arose on the BHP Billiton Olympic Dam electric slag cleaning furnace, where the slag tapholes would ‘self tap ’ or open unexpectedly. Investigations identified that the cause of these events was wear to the taphole and castable refractory.

NOMENCLATURE - CORE
Abstract During 2005 a safety issue arose on the BHP Billiton Olympic Dam electric slag cleaning furnace, where the slag tapholes would ‘self tap ’ or open unexpectedly. Investigations identified that the cause of these events was wear to the taphole and castable refractory.

(PDF) Improved Copper Flash Smelting at Olympic Dam
At the Olympic Dam flash furnace, molten particles separate into slag and blister copper (~99% copper) using t he direct to blis ter smelting tech nology .

BHP - Olympic Dam
WMC (Olympic Dam Operations) Pty Ltd is the management company, a wholly-owned subsidiary of BHP Billiton Limited, which took over WMC Resources in mid 2005. Initially BP Minerals Ltd was a 49% partner in the enterprise, but WMC took over BP Minerals share in 1993 for $315 million.

Monitoring Program Airborne Emissions - BHP
Monitoring Program – Airborne Emissions Olympic Dam Olympic Dam Document No. 2788 V.16 Page 3 of 13 2 DETAILED PROCEDURE 2.1 Smelter 2 emissions 2.1.1 Background Smelter 2 is one of the major sources of airborne emissions at Olympic Dam and comprises a Concentrate Feed Preparation Plant, Flash Furnace, Electric Slag Reduction Furnace, two ...

CFD MODELLING ASSISTANCE FOR THE DESIGN OF ELECTRIC ...
ABSTRACT During 2005 a safety issue arose on the BHP Billiton Olympic Dam electric slag cleaning furnace, where the slag tapholes would ‘self tap’ or open unexpectedly. Investigations identified that the cause of these events was wear to the taphole and castable refractory.

10t circular crane - Crane Services from Eilbeck Cranes
Temporary Construction Cranes for the Smelter No.2 Electric Slag Furnace Rebuild at Olympic Dam When client BHP Billiton wanted to utilise temporary special construction cranes for their Electric Slag Furnace Rebuild (ESFR) at Olympic Dam Mine Site (SA), they turned to Eilbeck Cranes and both worked closely together to bring to light a bespoke engineered solution for this special application.

Monitoring Program – Airborne Emissions Olympic Dam
Smelter 2 is one of the major sources of airborne emissions at Olympic Dam and comprises a Concentrate Feed Preparation Plant, Flash Furnace, Electric Slag Reduction Furnace, two Anode Furnaces and an Acid Plant. Copper concentrate is filtered and dried in the Feed Preparation Plant before being fed into the reaction shaft of the Flash Furnace.

Olympic Dam | Macmahon | MiningLink - The largest & most ...
Olympic Dam is the Largest Underground Mine in Australia ... In recent times a Svendala autogenous mill has been added along with extra electro-refining cells, a anode furnace gas-cleaning facility, an electric slag cleaning furnace, two counter-current decantation thickeners and …

Index 200 [www.gdmb.de]
Furnace Technology – 143 Composite Furnace Module Cooling Systems (CFM) in the Electric Slag Cleaning Furnace at Olympic Dam – 40 Faser mit geringer Biobeständigkeit und Temperatur von bis zu 1300 °C – 51 Laser shock peening – 250 New Technology Developments in the Production of Non-Ferrous Metals – 9 Porous Plugs – Degassing Technology in Alu-

Copper - Sulphuric Acid
The process is a continuous, multi-step process which produces blister copper from concentrates in three interconnecting furnaces. Concentrate and oxygen-enriched air (30-35% O2) enter the smelting furnace through vertical lances and are smelted to produce a matte of 65% to 69% Cu and low-copper slag.

FLUXING OPTIONS IN THE DIRECT- TO-BLISTER COPPER …
discarded. Therefore, metallic product of the slag cleaning furnace contains 5-10 % Fe and 12-18 % Pb, which are removed in a separate iron converting vessel before the copper is fed into anode furnace. In the Olympic Dam smelter, the slag is reduced to a point, where iron

BHP $350m investment in Olympic Dam to ... - Australian Mining
Jul 20, 2017 · BHP flagged it would carry out the maintenance program in yesterday’s operational review, which outlined that copper production at Olympic Dam was forecast to …
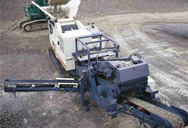
Sean Chelius - Program Manager - BHP | LinkedIn
View Sean Chelius’ profile on LinkedIn, the worlds largest professional community. ... Responsible for the project suite in the Olympic Dam Smelter Campaign portfolio. ... Slag Cleaning Furnace ...