
Wet Process for Manufacturing of Cement - …
In wet process if chalk is used, it is finely broken up and dispersed it in water in a wash mill. Wash mill is a circular pit consisting of revolving radial arms having rakes which breaks the solid materials into lumps. In similar wash mill, clay is also broken up and mixed with water. Now the two mixtures are pumped so as to mix in predetermined proportion and passed through a series of screens. The …

Cement Manufacturing - A Wet Process with the …
The cement manufacturing is done by majorly by two methods known as wet process and dry process depending on their mixing is done with water or without water. The wet process of cement manufacturing too popular for several decades because of the possibility of more accurate control while raw material mixing. After that, the dry process of raw material mixing gained momentum with the …

Wet Process of Cement Manufacturing - Cement …
The wet process of cement manufacturing refers to grinding raw material into slurry after mixing with water and then feeding them into the wet process kiln for drying and calcination and finally forming clinker. The slurry’s water content is usually between 32%-36%.

Explain dry and wet process of cement …
13.12.2018 · The specific feature of the wet process is that the raw materials are prepared in water whereas in the dry process the materials are ground and mixed dry. The flowsheet diagram of the wet process for manufacturing Portland cement is given in …

Dry Process for Manufacturing of Cement - …
In dry and semi dry processes for manufacturing of cement, the raw materials are crushed and fed in the correct proportions into a grinding mill. The raw materials are dried and reduced in size to a fine powder in to grinding mill. The dry powder is called the raw meal. The raw meal is pumped into a …

Cement Manufacturing Process: What is Cement …
Wet Process of Manufacturing of Cement. It is considered a better and convenient process for the manufacture of cement, especially where limestone of soft variety is available in abundance. We can discuss this process under three headings; preparation of slurry; burning or calcination; and treatment of clinker.

wet process of manufacturing of cement
The wet process of cement manufacturing involves adding water to finely crushed raw material such as limestone clay or iron ore in a proportion of 35 to 50 percent water to 50 to 65 percent raw material to make a slurry that is fed into a cement kiln whereas no. 【Get Price】 Energy and Cost Analysis of Cement Production Using the Wet and Dry Process. In Nigeria, approximately 40 to 50 per ...
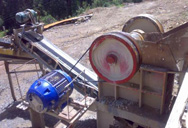
Cement Manufacturing Process | Phases | Flow …
Cement Manufacturing Process Phase V: Cooling and Final Grinding After passing out from the kiln, clinkers are cooled by mean of forced air. Clinker released the absorb heat and cool down to lower temperature. Released heat by clinker is reused by recirculating it back to the kiln.

What Is the Cement Manufacturing Process? (with …
12.05.2020 · Grinding is the next step in the cement manufacturing process, and it can occur in either wet or dry forms. Wet grinding involves combining all of the materials in a mill with water and grinding it into slurry. In contrast, dry grinding processes combine and grind the materials without water, creating a substance known as kiln feed.

Flow Chart Wet Process Of Cement Manufacturing
Cement manufacturing process flow chart i drying zones in the wet process the drying zone is comparatively larger than dry process in is because the raw material in slurry form is directly fed into the kiln which has more amount of water as shown in the figure it is the upper portion of the kiln.Contact now.

Difference Between Wet And Dry Process Of …
There are two different processes for manufacturing cement. wet process minerals are wet ground (by adding water) to form a slurry and then dried, dry process minerals are dry ground to form a powder-like substance. Both the processes are in use and have their own advantages and disadvantages. While in wet process grinding is easier, in the dry process there is a saving in fuel costs involved in drying up …

cement wet process manufacture figure of washmill
cement wet process manufacture figure of washmill. Page 1 of 7 Shrinkage of Concrete Concrete Technology in Focus Overview Concrete continues to be the most widely used construction material in the world because of . Get Price

Manufacture of Portland cement - University of Technology
• Clayey material – such as clay or shale clayey stones(soft), as a source of silica and alumina. Methods of cement manufacturing 1- Wet process ___ grinding and mixing of the raw materials in the existence of water. 2- Dry process ___ grinding and mixing of the raw materials in their dry state.

Wet Process Cement Manufacturing
The wet process of cement manufacturing involves adding water to finely crushed raw material such as limestone clay or iron ore in a proportion of 35 to 50 percent water to 50 to 65 percent raw material to make a slurry that is fed into a cement kiln whereas no water is added in the dry process. Cement Extraction And Processing Britannica

Cement Manufacturing - YouTube
31.07.2013 · Lime stone which provides calcium. Clay which provides aluminium and silica.Cement is manufactured by two methods they are. Wet process. Dry process. Now …

How Portland Cement is Made? Manufacturing …
Portland cement can be made by following two different processes – a dry one and a wet one. Joseph Aspdin first made portland cement in his kitchen stove in England in the 19th century. Lime and silica make up approximately 85% of portland cement. The materials that are commonly used are limestone, shells, chalk, shale, clay, slate, silica sand, and iron ore.