
Ball Mill Condition Monitoring- SPECIAL Mining …
Outotec millmapper is a globally patented technology and is the industry standard in mill liner condition monitoring and modeling accurate without any compromise over 7 million thickness points and hundreds of crosssections critical path components and hot spots …

Condition Monitoring of Ball Mill with HD …
Condition Monitoring of Ball Mill with HD Technologies. Robbert de Rouw | Team Leader Technical Support, SPM Instrument BV Save To Library . Introduction. Orcem in the Netherlands manufactures a special concrete called ECO2cem. One of the advantages of ECO2cem is that during the production process less CO2 is produced, making ECO2cem a very environment-friendly product. Orcem has two ...

A new model-based approach for power plant …
From then, the new research progress has been made in modelling and condition monitoring for Tube-ball mills and is reported in the paper. A mathematical model for Tube-ball milling process is developed by applying engineering principles combined with model unknown parameter identifications using a computational intelligent algorithm. The model describes the whole milling process from the mill idle …

Condition Monitoring of stone Mills | Dewesoft
By installing the Dewesoft Machine Condition Monitoring solution stone mills get a reliable solution to detect bearing issues for its press section rolls. The efficiency of the Dewesoft solution for detecting bearing failures - well in advance to the failure - also applies to other types of machinery in the industry such as blowers, conveyor belts, chippers, chip classifiers, refiners ...

SAG/Ball Mill Optimization | KnowledgeScape
GrindingExpert™ automatically adjust feed rate, mill speed and water addition to reduce upsets, eliminate grind-outs and increase tonnage in SAG / ball mills. We constantly maintain desired operating conditions by monitoring bearing pressure, power, recycle pebbles, mill density and mill acoustics. On average, expect a 3-6% increase in SAG mill throughput over an operator/DCS system.

Ball Milling - an overview | ScienceDirect Topics
Ball milling and ultrasonication were used to reduce the particle size and distribution. During ball milling the weight (grams) ratio of balls-to-clay particles was 100:2.5 and the milling operation was run for 24 hours. The effect of different types of balls on particle size reduction and narrowing particle size distribution was studied. The milled particles were dispersed in xylene to disaggregate the clumps. …

Ball Mills - Mineral Processing & Metallurgy
Ball Mill Charge volume. The mill power is approximately directly proportional to the charge volume within the normal range. When calculating a mill 40 % charge volume is generally used. In pebble and ball mills quite often charge volumes close to 50 % are used. In a pebble mill the pebble consumption ranges from 3—15 % and the charge has to be controlled automatically to maintain uniform power …

RESPONSE OF PRIMARY GRINDING MILL PERFORMANCE TO …
SAG mill and how the vibration response and hence mill operating conditions vary as a function of time, including during mill equipment failures such as a broken discharge grate. Opportunities for improved mill control based on the data from the on-line monitor are also discussed, as well as the implications in terms of mill processing and maintenance performance. Experience gained from the ...
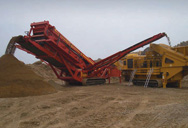
Optimization of mill performance by using
Optimization of mill performance by using online ball and pulp measurements Soon after a stop, a mill is a dangerous place to enter for the personnel tasked with taking measurements or samples. Crash stops are difficult to handle. The mill and all feed streams should be stopped simultaneously but, often, they are stopped around about the same time. Slurry

Ball Mill Trunnion Bearing Lube System
Maintaining the ball mill charge and monitoring the feed rate will help to ensure maximum efficiency of the grinding system. System interlocks monitor the operating condition of the grinding mill and will shut down the mill if conditions deviate from operating parameters. Regular monitoring of the feed rate, ore hardness, mill power draw, mill charge volumes (charge weights), and periodic visual …

MillMapper Liner Wear Monitoring - Outotec
Outotec MillMapper is a globally patented technology and is the industry standard in mill liner condition monitoring and modeling. Accurate without any compromise. Over 7 million thickness points and hundreds of cross-sections, critical path components, and hot spots detected from every scan; Proven and trusted solution

Condition Monitoring - Multotec
Condition monitoring from Multotec comprises a range of innovative condition monitoring products that are designed and manufactured to extend the lifespan of your mineral processing equipment.. Our condition monitoring products give you real-time, actionable data that ultimately monitors your wear rates against your productivity.