
Factors that Impact Efficiency Improvement of …
Generally speaking, the factors that impact the efficiency improvement of ball mill are as follows: (1)Reduction Gear. Increasing the rotation speed is the key to improve working efficiency of ball mill. For this reason, properly improving the reduction gear can also have a certain effect, and the qualified ore dressing plant can install frequency changer to adjust the rotation speed.

5 Ways To Improve Grinding Efficiency Of Ball …
Another factor that affects ball mill cement grinding efficiency and effectiveness as it relates to a specific material size distribution is the circulating load. It has been observed with increased circulating load and classifier efficiency; there is an increase in the grinding efficiency. When the circulating load is increased, it results in a reduction in overgrinding, and it offers the media a more effective size …

The Factors That Restrict the Improvement of the …
The Ball Mill’s working efficiency directly affects the concentrator economic benefits of the Beneficiationfactories. Therefore improve the efficiency of the mill is very important.Generally speaking, the factors restricting the improvement of the ball mill efficiency as following:1. The electric currentFor ball mill, enlarging the current is to increase the rotate . . .

ball mill efficiency improvement
ball mill efficiency improvement Improving Overall Concentrator Performance with Stirred Milling In the last 100 years, ball mills are traditionally used for this stage although they are known to be the least energy efficient devices.

Development and Efficiency Improvement of Ball …
Loading capacity of the grinding media has a major impact on the efficiency improvement of ball mill. If the loading capacity is too small, materials impacts and grinding will be small, while excessive load reduces feeding, grinding interaction will be increased. The proportion of material and water should be appropriate, eventually see the water rate of mud and liquidity to set water yield. In general, the …

Analysis of Ways to Increase Ball Mill Efficiency - …
The second one is to make improvement in grinding system. The third one is to set a high efficiency separator which selects the final powder as much as possible. This way reduces the powder retrieval rate as well as the mill burden. Any of the three methods listed above can greatly improve the ball mill output. If given conditions, users can integrate the three ways to get a better result ...

ball mill efficiency improvement - …
ball mill efficiency improvement Solutions Just Right For You. The ball mill products manufactured by Henan Bailing Machinery are of reliable structure stable running high efficiency and energy-saving The ball mill application is pretty wide such as the cement silicate products new building material refractory material stone fertilizer black and non-ferrous metal beneficiation and glass ...

Factors Affecting Ball Mill Grinding Efficiency
The same source of synergy found in Turner’s “optimized load” principle can also be applied to ball milling through suitable application of grinding mechanisms in conjunction with the other previously described factors that effect ball mill efficiency. While examples of ball mill efficiency improvements may be far less dramatic, they are none the less as significant in their own realm.

The energy efficiency of ball milling in …
Earlier work by Fuerstenau and Kapur on the comminution of quartz in a single-particle roll mill and in a dry ball mill showed the energy efficiency of ball mill comminution to be 22%. Thus, as a mechanical device for producing fine particles, the ball mill is reasonably efficient energetically. Since single-particle breakage always produces a product with a distribution modulus of unity, using this as a …

Energy efficiency of cement finish grinding in a …
2.3. Choice of the operating parameters for ball milling. Steel balls with a density of 7800 kg/m 3 were used. The total load of balls was calculated by the formal fractional mill volume filled by balls (J), using a bed porosity of 0.4.The fractional filling of voids between the balls (U) can be calculated by U = fc / 0.4J; fc is the formal fractional mill volume filled by powder using a ...

MODULE #5: FUNCTIONAL PERFOMANCE OF BALL MILLING
For any process, including ball mill circuits, we can say that output equals input multiplied by efficiency*. Output = Input x Efficiency In a ball mill circuit, the "output" can be defined as the production rate of fines of the circuit. As for any output, ball mill circuit output is a …

Improvement of cement performances through the use of ...
Improvement of cement performances through the use of grinding aids in vertical roller mill P.D’Arcangelo, M.Magistri – Mapei SpA, Milan, Italy Abstract Due to the stringent requirement of energy saving, the use of vertical roller mills for cement grinding is now common. Even though the reliability and operation stability of modern VRM is very good, there is still room for further ...

(PDF) DESIGN AND FABRICATION OF MINI BALL …
A numerical dynamic-mechanical model of a planetary ball-mill is developed to study the dependence of process efficiency on milling parameters like ball size and number, jar geometry and velocity ...
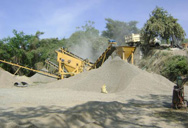
Ball Mill Design/Power Calculation
A wet grinding ball mill in closed circuit is to be fed 100 TPH of a material with a work index of 15 and a size distribution of 80% passing ¼ inch (6350 microns). The required product size distribution is to be 80% passing 100 mesh (149 microns). In order to determine the power requirement, the steps are as follows: Example Calculation. A motor with around 1400 Horse Power is calculated ...

Bond Grinding Circuit Efficiency - ceecthefuture.org
Bond Grinding Circuit Efficiency • The Bond Work Index equation • Ore test WI • Circuit operating WI • Grinding circuit WI Efficiency • Example calculations • Data base examples • Conclusions 2. 2/20/2014 2 The Bond Equation 3 The equivalent energy needed to go from very large rock to 100 um, i.e. a standard amount of size reduction! The Bond Equation 4. 2/20/2014 3 The Bond ...

PROCESS DIAGNOSTIC STUDIES FOR CEMENT MILL …
Ball mills are predominantly used machines for grinding in the cement industry. Although ball mills have been used for more than one hundred years, the design is still being improved in order to reduce the grinding costs. HOLTEC has undertaken Performance Optimisation of the cement grinding circuits by doing process diagnostic studies in many cement plants. The stone describes the approach for ...

high efficiency gold ball mill for gold processing …
Energy Saving Ball Mill. A high efficiency and energy saving ball mill with rolling bearing.Cylindrical energy saving grid ball mill is lined grooved ring plate which increases the contact surface of ball and ore and strengthens the grinding. Get Price. ball mill gravity thickener,laboratory flotation cell . At Present, Xinhai business includes Mineral Processing EPC, Wear-Resistant stone ...