
how to increase temp in ball mill - …
Temperature progression in a mixer ball mill SpringerLink22/4/2016 The influence of the operating frequency, the milling ball and grinding stock filling

How To Control Ball Mill Cement Temp - …
High Exit vent temp at cement mill outlet Page 1 of 1. 2015-11-02· High Exit vent temp at cement mill outlet. We have open circuit ball mill grinding OPC 43 grade, feed moisture 2% max, Inlet temp 35 Deg C and outlet temp we are getting around 90 to 95 deg C, what could be the reason of high temp at mill outlet, since we have not supplied hot gas at feed, can anybody suggest the possible ...

Temperature progression in a mixer ball mill | …
22-4-2016 · Mechanochemistry using ball mills is a promising technique with applications in organic and inorganic chemistry as well as material sciences [1–4].During ball milling, up to 80 % of the energy that is generated in the mill is dissipated as heat [].This is why measurement and control of the temperature in the ball mills is important, for example, if heat-sensitive products are formed that ...
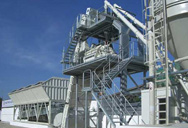
increase the efficiency of ball mills - cuppen …
increase the efficiency of ball mills. optimizing your sag mill operation international optimizing your sag mill directly to large ball mills, the energy efficiency of the concentrator was and a further increase in load inside the mill how to increase temp in ball mill efficiency increase in ball mill five steps to. …

Cement mill - Wikipedia
A cement mill (or finish mill in North American usage) is the equipment used to grind the hard, nodular clinker from the cement kiln into the fine grey powder that is cement.Most cement is currently ground in ball mills and also vertical roller mills which are more effective than ball mills.

how to improve capacity of ball mills in nigeria
How to improve capacity of ball mills how to increase crushing capability of ball mill how to increase cement mill capacity crusher before a ball mill the capacity crusher before a ball mill the capacity can be greatly increased 2 The cement ball mill of the work there are all together three shortcuts to increase the productivity of ball mill ...

How to Improve the Production of Ball Mills?
Ball mill as a kind of popular grinding and ore beneficiation equipment is widely used in cement manufacturing, silicate products, construction materials, refractory and other industries. It is ...

how to increase ball mill output
The SAG Mill is a machine added by Ender IO It uses Micro Infinity (I) to grind (or mill) items into their crushed variants like Ores into Dusts The SAG Mill has four output slots recipes can have 1-4 different outputs with different chances of obtaining those outputs Uniquely the SAG Mill can use Grinding Balls made from various materials to increase energy efficiency (resulting in

Factors Affecting Ball Mill Grinding Efficiency
The following are factors that have been investigated and applied in conventional ball milling in order to maximize grinding efficiency: a) Mill Geometry and Speed – Bond (1954) observed grinding efficiency to be a function of ball mill diameter, and established empirical relationships for recommended media size and mill speed that take this factor into account. As well, mills with different ...

Calculate and Select Ball Mill Ball Size for Optimum …
In Grinding, selecting (calculate) the correct or optimum ball size that allows for the best and optimum/ideal or target grind size to be achieved by your ball mill is an important thing for a Mineral Processing Engineer AKA Metallurgist to do. Often, the ball used in ball mills is oversize “just in case”. Well, this safety factor can cost you much in recovery and/or mill liner wear and ...

Ball Mill: Operating principles, components, Uses ...
Several types of ball mills exist. They differ to an extent in their operating principle. They also differ in their maximum capacity of the milling vessel, ranging from 0.010 liters for planetary ball mills, mixer mills, or vibration ball mills to several 100 liters for horizontal rolling ball mills.

Cement mill notebook - LinkedIn SlideShare
Raw mills usually operate at 72-74% critical speed and cement mills at 74-76%. 3.2 Calculation of the Critical Mill Speed: G: weight of a grinding ball in kg. w: Angular velocity of the mill tube in radial/second. w = 2*3.14*(n/60) Di: inside mill diameter in meter (effective mill …

Make a Ball Mill in 5 Minutes : 4 Steps - Instructables
Make a Ball Mill in 5 Minutes: This is for all the pyro nuts that I came across on Instructables. This can be used to grind chemicals to a very fine stone or to polish rocks.Wiki says "A ball mill is a type of grinder used to grind materials into extremely fine powder for use i...

Optimization of mill performance by using - SciELO
Optimization of mill performance by using online ball and pulp measurements Soon after a stop, a mill is a dangerous place to enter for the personnel tasked with taking measurements or samples. Crash stops are difficult to handle. The mill and all feed streams should be stopped simultaneously but, often, they are stopped around about the same time.

High Exit vent temp at cement mill outlet - Page 1 …
2-11-2015 · High Exit vent temp at cement mill outlet. We have open circuit ball mill grinding OPC 43 grade, feed moisture 2% max, Inlet temp 35 Deg C and outlet temp we are getting around 90 to 95 deg C, what could be the reason of high temp at mill outlet, since we have not supplied hot gas at feed, can anybody suggest the possible reason please, which helps to take necessary action.

How to Ball Mill Chemicals Safely — Skylighter, Inc.
How to safely and effectively use a ball mill to grind pyrotechnic chemicals and black powder. ... I’m also including how-to info for a few other milling accessories that will increase your milling productivity. ... mill temp: 57 degrees F 20 minutes into run, mill temp: 64 degrees F 30 minutes: 73 degrees

Ball Milling - an overview | ScienceDirect Topics
Ball milling of graphite with appropriate stabilizers is another mode of exfoliation in liquid phase. 21 Graphite is ground under high sheer rates with millimeter-sized metal balls causing exfoliation to graphene (Fig. 2.5), under wet or dry conditions.For instance, this method can be employed to produce nearly 50 g of graphene in the absence of any oxidant. 22 Graphite (50 g) was ground in ...

Ball Mill Design/Power Calculation - LinkedIn
12-12-2016 · Ball Mill Power Calculation Example A wet grinding ball mill in closed circuit is to be fed 100 TPH of a material with a work index of 15 and a size …

HOW BALL MILL WORKS? - energosteel.com
The ball mill is a hollow drum closed with loading and unloading end caps, filled with grinding media and rotated around its axis.The drum of the ball mill (Pic. 1) is a hollow cylinder of steel, lined inside with armor lining plates which protect it from impact and friction effects of the balls and the grinding material.

Ball Mills - an overview | ScienceDirect Topics
Oleg D. Neikov, in Handbook of Non-Ferrous Metal Powders, 2009. Tumbling Ball Mills. Tumbling ball mills or ball mills are most widely used in both wet and dry systems, in batch and continuous operations, and on a small and large scale.. Grinding elements in ball mills travel at different velocities. Therefore, collision force, direction and kinetic energy between two or more elements vary ...