
Energy Balance Over A Ball Mill - plaidwebshop.nl
Energy Balance Grinding Mill Ball Mill Heat Balance . Ball Milling Machine Energy Balance Grinding Mill Me. Ball milling machine energy balance grinding mill china the high energy ball mill e max and mm 500 were developed for grinding with the highest energy input the innovative design of both the mills and the grinding jars allows for continuous grinding down to the nano range in the shortest
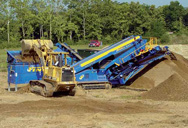
Ball mill - Wikipedia
A ball mill is a type of grinder used to grind, blend and sometimes for mixing of materials for use in mineral dressing processes, paints, pyrotechnics, ceramics, and selective laser sintering.It works on the principle of impact and attrition: size reduction is done by impact as the balls drop from near the top of the shell. A ball mill consists of a hollow cylindrical shell rotati

Temperature progression in a mixer ball mill | …
22-4-2016 · Mechanochemistry using ball mills is a promising technique with applications in organic and inorganic chemistry as well as material sciences [1–4].During ball milling, up to 80 % of the energy that is generated in the mill is dissipated as heat [].This is why measurement and control of the temperature in the ball mills is important, for example, if heat-sensitive products are formed that ...

The energy efficiency of ball milling in …
Instead of defining comminution efficiency in terms of the surface free energy of the solid, we propose that it be defined as a relation between the specific energy to produce the given amount of new surface in single-particle comminution with that required for the comminution device under consideration: (1) Energy efficiency =[E m (SP)/E m (Mill) to produce same specific surface]100 where E m ...

Factors Affecting Ball Mill Grinding Efficiency
The following are factors that have been investigated and applied in conventional ball milling in order to maximize grinding efficiency: a) Mill Geometry and Speed – Bond (1954) observed grinding efficiency to be a function of ball mill diameter, and established empirical relationships for recommended media size and mill speed that take this factor into account. As well, mills with different ...

Ball Mills - an overview | ScienceDirect Topics
Oleg D. Neikov, in Handbook of Non-Ferrous Metal Powders, 2009. Tumbling Ball Mills. Tumbling ball mills or ball mills are most widely used in both wet and dry systems, in batch and continuous operations, and on a small and large scale.. Grinding elements in ball mills travel at different velocities. Therefore, collision force, direction and kinetic energy between two or more elements vary ...

Design Method of Ball Mill by Sumitomo stone Co., Ltd ...
This relationship was successfully used for the scale-up of a rocking ball mill, and the optimum design and operating conditions for the rocking ball mill could be estimated by the specific impact energy of the balls cal-culated by a computer simulation. Sumitomo stone Co., Ltd. Process & Production Technology Center Makio KIMURA Masayuki NARUMI

Cement mill - Wikipedia
A cement mill (or finish mill in North American usage) is the equipment used to grind the hard, nodular clinker from the cement kiln into the fine grey powder that is cement.Most cement is currently ground in ball mills and also vertical roller mills which are more effective than ball mills.

Ball Mills - Mineral Processing & Metallurgy
In all ore dressing and milling Operations, including flotation, cyanidation, gravity concentration, and amalgamation, the Working Principle is to crush and grind, often with rob mill & ball mills, the ore in order to liberate the minerals. In the stone and process industries, grinding is an important step in preparing raw materials for subsequent treatment.

High-Energy Ball Mill Processing - IPEN
High-Energy Ball Mill Processing Edval G. Araújo, Ricardo M. Leal Neto, ... high-energy milling process, done dry, for producing metal-matrix composite powders with ... when the heat generated by the system exceeds the dissipation heat rate, this exceeding energy could be used as an activation energy for the reaction that can propagate

(PDF) DESIGN AND FABRICATION OF MINI BALL …
DESIGN AND FABRICATION OF MINI BALL MILL. ... for recovery in the separation process, it is crucial to run the mills at the best operating ... (energy) of the high energy ball milling has been ...

Ball Mill Design/Power Calculation - LinkedIn
12-12-2016 · If P is less than 80% passing 70 microns, power consumption will be. Ball Mill Power Calculation Example. A wet grinding ball mill in closed circuit is to be fed 100 TPH of a …

Best energy consumption - International Cement …
For ball mills, ball charge level, lining and diaphragm condition must be monitored and maintained in near-optimum condition. Mill stops, defined as mill motor off, and measured by mean time between failures (mtbf), are frequently poorly recorded and the resolution of underlying issues is …

high energy ball milling process - hausbau …
While a number of ball mills ingenious milling devices were developed early in the cen-tury, the one high energy ball mill that has been adopted by industry was invented by Szegvari in 1922, in order to quickly attain a fine sulphur dispersion for use in vulcaniza-tion of rubber.

Grinding in Ball Mills: Modeling and Process Control
Keywords: Ball mills, grinding circuit, process control. I. Introduction Grinding in ball mills is an important technological process applied to reduce the size of particles which may have different nature and a wide diversity of physical, mechanical and stone characteristics. Typical examples are the various ores, minerals, limestone, etc ...

Hammer Mill: components, operating principles, …
Disadvantages of Hammer Mill. Not recommended for the fine grinding of very hard and abrasive material due to excessive wear. Not suitable for low-melting sticky or plastic-like material due to heat generation in the mill head as a result of mill fouling. The mill may be choked if the feed rate is not controlled, leading to damage.

(PDF) High Energy Ball Mill Processing - …
The high-energy ball mill processing can be divided in three main ... It is believed that the phase transformations occurring during ball milling are negative heat of ... No process control agent ...
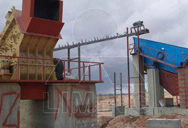
high energy ball milling process - pelsdieren.be
Planetary Ball Mill Mechanism resto-osaka. Planetary Ball Mills 101 Union Process. With the planetary ball mills and the new high energy ball mill Emax, RETSCH offers two types of Planetary Ball Mills…

High Energy Ball Milling & How It Works | Union …
High Energy Ball Milling. In discussions on high energy ball milling, the more generic term "ball mills" is often used in place of the terms "stirred ball mills" or "Attritors," but the differences between the types of mills are quite distinct.

Variables in Ball Mill Operation | Paul O. Abbe®
Variables in Ball Mill Operation. ... quote online or call 630-350-3012 to speak with an expert at Paul O. Abbe® to help you determine which design and size mill would be best for your process. See our Size Reduction Options: Steel Ball Mills. Benefits of Tumble Milling: ... more of the energy goes into milling and less wasted as heat.