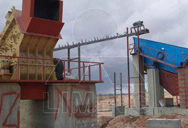
Low Heat Cement- Composition, Properties, Uses …
Low heat cement is a special tailored cement which generates low heat of hydration during setting. It is manufactured by modifying the stone composition of normal Portland cement. In this article we discuss about the composition, properties, characteristics, uses and advantages of low heat cement.

Low Heat Cement | The Construction Civil
Low Heat Cement as the name indicates these type of cement is used inorder to reduce the amount of heat evolved during setting. But how the heat evolved during setting can be reduced ? Yes, the heat during setting can be reduced by lowering the percentage of tri-calcium aluminate C3A of about 5% an higher percentage of di-calcium silicate C2S of about 46% .

Low Heat Portland Cement, Properties, Uses And ...
The process of hydration is slow and the consequent rate of heat generation is also low. It is manufactured from the ingredients of specially selected cement clinker, gypsum and ground granulated blast furnace slag, which result in significantly lower heat generation during the process of hydration than in a typical Portland cement.

manufacturing process of low heat cement
Jun 3, 2014 Waste Heat Recovery in the Cement Process . stems from low manufacturing cost, and the fact that it can be produced locally from widely . Patent WO2011051962A2 - A process for manufacturing white . May 5, 2011 The invention provides a process for manufacturing white cement which In this system efficiency gain of upto 50% for low temperature heat. Portland Composite Cement (PCC ...
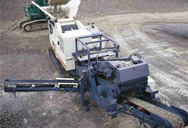
process of manufacturing of low heat cement
process of manufacturing of low heat cement Variation of Feed stone Composition and Its Effect on The raw materials for Portland cement production are the mixture (as fine powder in the Dry process) of minerals B Burning Process In modem systems of cement manufacture the retention time of the material in the kiln is 30 to 40 minutes too low combination of the raw material components may be
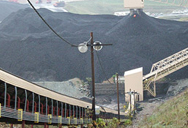
Low Heat Cement: Less Susceptible to Cracks!
Low heat cement has low value of setting time as compared to OPC, as it sets slowly; the heat of hydration is also released slowly. As per IS code 12600 -1989, the initial setting time of low heat cement is 60 minutes and the final setting time is 600 minutes. It …
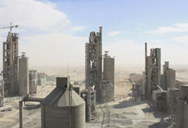
Cement Manufacturing Process | Phases | Flow …
When material reaches the lower part of the kiln, it forms the shape of clinker. Cement Manufacturing Process Phase V: Cooling and Final Grinding. After passing out from the kiln, clinkers are cooled by mean of forced air. Clinker released the absorb heat and cool down to lower temperature. Released heat by clinker is reused by recirculating it back to the kiln. This too saves energy.
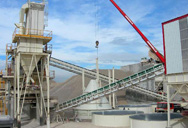
What is the reason to use low heat cement in the ...
Hydration of cement is an exothermic process that produces large quantity of heat. In a mass concrete structure like dams, the rate of dissipation of heat of hydration from the surface is much lower than that generated. It causes rise in temperatu...
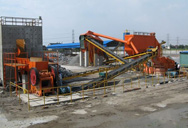
process of manufacturing of low heat cement
how the low heat cement process ... 40015 of 10000 -process of manufacturing of low heat cement,cost of process of manufacturing of low heat cement,China Company ... Chat Online. Pre: mobile gravel equipment Next:used grinding machines. Free Chat for GET PRICE ! Products. China Clay beneficiation process . process of marble mine. finex process iron ore spec. used liming cone …
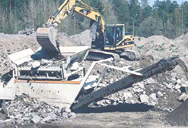
Cement: stages of manufacture of artificial …
CEM III (blastfurnace cement) and CEM V (composite cement): cements giving off low heat during hydration and with low sulfate contents, used for underground works in aggressive environments or for maritime works. CEM IV (pozzolanic cements): cements using mineral ingredients of volcanic origin that display hydraulic properties. We manufacture and market this kind of cement only in Italy ...
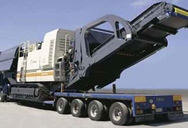
low heat cement - Deutsch-Übersetzung – Linguee Wörterbuch
Low heat common cement according to DIN EN 197-1/A1 (LH cement) vdz-online.de. vdz-online.de. ... On-going development process has developed the original cardboard production that started more than 40 years ago into heat treatment plants for plaster and cement-bound building boards, ceiling and facade elements, filtration and bonded fiber fabrics, leather fiber strips, ecological insulating ...
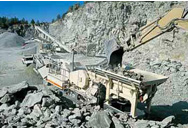
Cement Manufacturing Process: What is Cement …
Cement manufacturing process & what is cement made of, it can be discussed conveniently under two headings: Selection of Raw materials and manufacturing methods. Raw Materials of Cement. Most important raw materials (what is cement made of) required in the manufacture of Portland Cement are: Limestone, Clay, Gypsum, Fuel, and Water (in wet method).

How Cement Is Made - Portland Cement …
The heated air from the coolers is returned to the kilns, a process that saves fuel and increases burning efficiency. After the clinker is cooled, cement plants grind it and mix it with small amounts of gypsum and limestone. Cement is so fine that 1 pound of cement contains 150 billion grains. The cement is now ready for transport to ready-mix concrete companies to be used in a variety of construction …

Setting Time of Cement Concrete - Stages and …
The process of setting starts after the addition of water. In this process the four compounds of cement (C 3 S, C 2 S, 3CA1, 4CAFe) get hydrated. C 3 S compound of cement gets hydrated and form a complex hydro silicates. 2. Colloidisation Stage

low heat - Deutsch-Übersetzung – Linguee Wörterbuch
Viele übersetzte Beispielsätze mit "low heat" – Deutsch-Englisch Wörterbuch und Suchmaschine für Millionen von Deutsch-Übersetzungen.
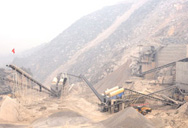
The cement kiln - Understanding Cement
Wet process kilns. The original rotary cement kilns were called wet process kilns. In their basic form they were relatively simple compared with modern developments. The raw meal was supplied at ambient temperature in the form of a slurry. A wet process kiln may be up to 200m long and 6m in diameter. It has to be long because a lot of water ...
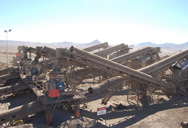
Industrial trial production of low energy belite …
The calcining process for the CaCO 3 component of the raw feed absorbs a large amount of the heat (≈1350 kJ/kg clinker). The net heat balance for ordinary Portland cement clinker (OPC) manufacture has been calculated to be 1674–1799 kJ/kg clinker for different raw mixes by various authors , , . The heat required in practice (3100–3600 kJ ...
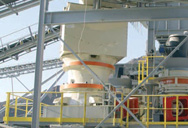
(PDF) Low Heat Concrete | Frank Papworth - …
This stone summarises the factors controlling concrete’s heat of hydration, the likely problems caused by the heat generated and the available solutions using blended cements. The heat of hydration of various silica fume and slag cement blends are

Low-heat cement | Article about low-heat cement …
In order to achieve the compensation effect on the temperature shrinkage of hydraulic concrete by using the delayed expansion of periclase in the LHC cement, LHC clinker was prepared under different calcination conditions, and the influence of crystal size of periclase on the hydration and expansion of the self-prepared low-heat cement was studied in this paper.
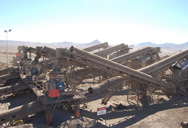
Technology of Concrete with Low Generation of …
Conclusion Based on the above-mentioned methodological procedure, starting with tests on simpler systems, which are cement pastes through concrete up to the development of a 3D model using the finite element method, it is possible to create a complex concrete design with low development of hydration heat. In addition to the proposal for the composition, then using the mentioned procedure, it ...