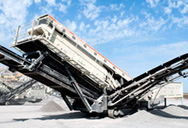
Iron ore slurry filtering solutions
Iron ore slurry filtering solutions Iron ore is ground to finer particle sizes through different grinding systems. Large grinding mills using grinding ball media are one of the most common and particularly in pelletizing plants where finer particle size are required for the pelletizing process.
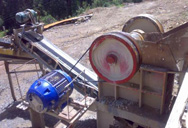
Iron Ore Processing for the Blast Furnace
the ore is reduced to 3/4" or less, it moves out of the mill in a slurry solution. The mill discharge is screened at 1/4" on trommel screens attached to the mill. Ore smaller than 1/4" is pumped in slurry solution to the wet cobber magnetic separator, which begins the process of separating the iron from the non-iron material.

Heavy Duty Slurry Pumps for Hard Rock Mining Industries
Iron Ore. From mine dewatering to mill discharge, concentrators, carbon-in-leach, agglomerators, and tailings, our slurry pumps are doing the job. The toughest conditions are met with the most wear-resistant and rugged pumps Schurco Slurry manufactures. Schurco Slurry pumps can be found all over the world pumping highly abrasive slurries wherever iron, copper, gold, silver, nickel, and all …
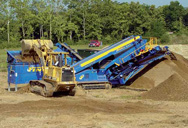
iron ore grinding slurry managment - pelsdieren.be
iron ore grinding slurry managment. Iron ore Wikipedia The Lower-grade sources of iron ore generally require beneficiation, using techniques like crushing, milling, gravity or heavy media separation, screening, and silica froth flotation to improve the concentration of the ore and remove impurities.
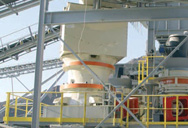
Iron Ore,Production Process of Iron Ore,Iron Ore ...
Production Process of Iron Ore Generally, the processing of iron ore needs several processing stages, including crushing, grinding, ore beneficiation, concentrating, drying, etc. The equipments for iron ore beneficiation is consisted of Jaw Crusher, Ball Mill , Classifier, Magnetic Separator, Flotation Machine, Concentrator Machine and Dryer.
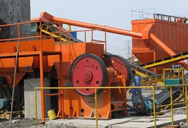
Iron processing | Britannica
Iron processing, use of a smelting process to turn the ore into a form from which products can be fashioned.Included in this article also is a discussion of the mining of iron and of its preparation for smelting. Iron (Fe) is a relatively dense metal with a silvery white appearance and distinctive magnetic properties. It constitutes 5 percent by weight of the Earth’s crust, and it is the ...
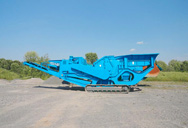
Hematite Processing by Flotation
Direct shipping of high grade iron ore, because of depletion or partial depletion of reserves, or high costs of operation has forced operators to use some means of beneficiation to produce an acceptable product with the lower grade iron ore reserves. Deposits of comparatively lower grade iron ore that remain relatively untouched or by-passed, are now most important because of increase in ...
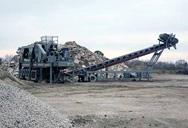
Iron ore pelletizing systems - liming
Both straight grates and grate kilns dry the pellets out in a drying section, then bring the pellets up to a temperature of about 800-900 °C in a preheat zone, then finish the induration process at roughly 1200-1350 °C. The pellets are then cooled to a suitable temperature for transporting to a load out facility.

SEPARATION EXPERTISE FOR YOUR SUCCESS IN THE IRON …
As the demand for iron ore rises, so does the need for higher capacities. Maybe it’s processing huge volumes of low-grade ore with minimal residual moisture. Or doubling your throughput with a high-capacity filter press. In either case, we have an innovative solution to make it both possible and profitable. Filter press Horizontal vacuum belt ...
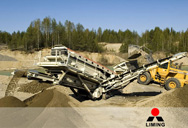
Long Distance Pipeline Transportation of Ore Slurry
MMX, Iron Ore Slurry Pipeline, Brasil, 550 kms Da Hong Shan, Iron Ore Slurry Pipeline, China, 171 kms Paragominas, Bauxite Slurry Pipeline, Brasil, 244 kms Samarco, Iron Ore Slurry Pipeline, Brasil, 396 kms Simplot, Phosphate Pipeline, USA, 100 kms New Zealand Steel, Ironsand Concentrate Pipeline, New Zealand, 18 km

Ernest Henry Mining: Magnetite Processing
recovered from the ore in the EHM concentrator, water is added to the concentrator tailings to form slurry of suitable density for the rougher magnetic separator circuit in the magnetite extraction plant. Ernest Henry Mining: Magnetite Processing For more information contact Vicki Wilson, Senior Community Relations Advisor, EHM on 07 4769 4578.

Advances in Low Grade Iron Ore Beneficiation
iron ore is expected to rise by more than 200 million tonne per year to meet the internal demand & export. This additional requirement of iron ore will need beneficiation of low grade ore/fines to get the major portion of increased demand. This stone deals in brief to use of available methodologies for beneficiation of iron ore in Indian context.
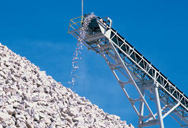
Iron ore mining and dressing - tec-science
Ore processing (or ore dressing) is the separation of iron ore from gangue in order to optimize the blast furnace process! In principle, the undesirable gangue can never be completely separated from the iron ores during ore dressing. This means that a certain amount of unwanted elements always enters the blast furnace process.
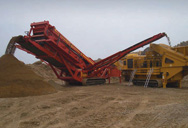
pH in Iron Ore Slurry + NaOH Solution | Yokogawa America
iron ore slurry without dispersant addition. In stable dispersion of fine particles is the pre-requisite for the selective flocculation technique involving separation of ultra-fine valuable particles from the gangue.

Beneficiation of Iron Ores – IspatGuru
This process is primitive and widely used in lumpy iron ore processing to dislodge and remove friable and soft lateritic materials, fine materials and limonitic clay particles adhering to the ore. Wet scrubbing is also useful in hard and porous ores, which invariably have cavity/pores filled with clayey material that need substantial removal.
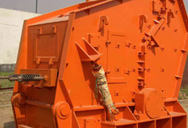
pH in Iron Ore Slurry + NaOH Solution | Yokogawa Europe
iron ore slurry without dispersant addition. In stable dispersion of fine particles is the pre-requisite for the selective flocculation technique involving separation of ultra-fine valuable particles from the gangue.

Slurry Piping Performance - Beaver Process Equipment
Iron Ore Processing Plant. The audit process identified several high wear areas and the cause of daily breakdowns. After installing the recommended products and making small changes we no longer have those regular leakages, spillage and slips.
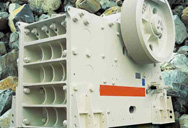
Slurry rheology and tailings pumping design - Pump ...
Jul 12, 2013 · An iron ore processing plant located in the Pilbara Region of Western Australia was undergoing a raise in the wall height for the storage facility to increase the long term capacity. A series of slurry rheology tests had been conducted and a relationship of slurry shear rate and shear stress values were determined.