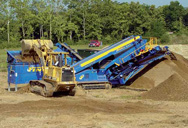
Best way to determine the ball-to-powder ratio in …
Then, the optimal mass ratio of ball to powder in ball mill is 7.5*24/(2.5*17.6)= 4.09 to 7.5*21/(2.5*11.2) = 5.63.
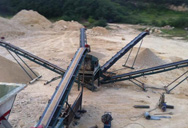
Why the ball to powder ratio (BPR) is insufficient …
The ball to powder ratio (BPR) is a processing parameter that is frequently used in both mechanical (ball) milling and mechanical alloying. A number of recent studies provided the BPR as a principal milling parameter while neglecting other parameters, such the vial volume, the diameter and quantity of milling balls and the powder mass. In this experiment, different batches of magnesium hydride powder …
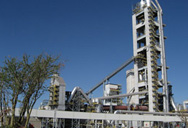
How to calculate ball to powder ratio? - …
Then, concerning the ball to powder ratio as well other parameters like milling time and rotation speed it depends on which particle size and stone size (nanostructure) you are interested. Higher ...
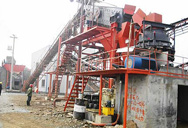
milling ball to powder ratio – Grinding Mill China
Mechanical milling of aluminum powder using plane, M Ramezani, T Neitzert, Mechanical milling of aluminum powder using planetary ball milling process, Journal , Summary of milling parameters Time Ball No Ball size (mm) Stearic ac Methanol Speed (rpm) Ratio (B/P) 05 hr 100 10 » Learn More. Why the ball to powder ratio (BPR) is insufficient for ,
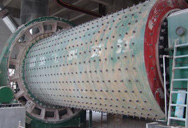
ball to powder ratio ball mill - klimaatwebsite.be
ball mill ball to powder ratio educationcareinWhy the ball to powder ratio (BPR) is insufficient for describing the , The ball to powder ratio (BPR) is a processing parameter that is frequently used in both mechanical (ball) milling and mechanical alloying A number of recent s More details » Get PriceEffect of Ball to Powder Weight Ratio on the ,Effect of Ball to Powder Weight Ratio on the ...
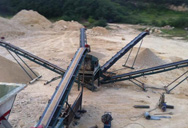
Why the ball to powder ratio (BPR) is insufficient …
The ball to powder ratio (BPR) is a processing parameter that is frequently used in both mechanical (ball) milling and mechanical alloying. A number of recent studies provided the BPR as a principal milling parameter while neglecting other parameters, such the vial volume, the diameter and quantity of milling balls and the powder mass. In this experiment, different batches of magnesium hydride powder …
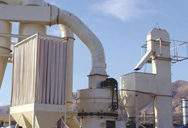
Calculate and Select Ball Mill Ball Size for …
In Grinding, selecting (calculate) the correct or optimum ball size that allows for the best and optimum/ideal or target grind size to be achieved by your ball mill is an important thing for a Mineral Processing Engineer AKA Metallurgist to do. Often, the ball used in ball mills is oversize “just in case”. Well, this safety factor can cost you much in recovery and/or mill liner wear and ...
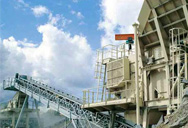
Ball Mill Design/Power Calculation - LinkedIn
12.12.2016 · Ball Mill Power Calculation Example A wet grinding ball mill in closed circuit is to be fed 100 TPH of a material with a work index of 15 and a size …
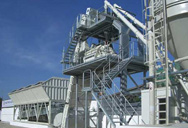
How to Size a Ball Mill -Design Calculator & …
2) Ball milling – a ball mill with a diameter of 2.44 meters, inside new liners, grinding wet in open circuit. When the grinding conditions differ from these specified conditions, efficiency factors (Rowland and Kjos, 1978) have to be used in conjunction with equation 1.
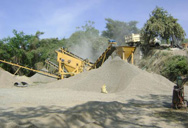
Ball Mill Design/Power Calculation
A wet grinding ball mill in closed circuit is to be fed 100 TPH of a material with a work index of 15 and a size distribution of 80% passing ¼ inch (6350 microns). The required product size distribution is to be 80% passing 100 mesh (149 microns). In order to determine the power requirement, the steps are as follows: Example Calculation. A motor with around 1400 Horse Power is calculated ...

ball mill for powders - cuppen-psychologen.nl
How to calculate ball to powder ratio? - ResearchGate. For example grinding with planetary ball mill makes a wide PSD which is not desired I want o mill silica powder (D90=100 , D10=50 micron) to fine powder (D9010 , D505, D102 micron). 【Get Price】 (PDF) On the Use of Ball Milling for the Production of. In the present research work the mixture of boron carbide and graphite ceramic powders ...
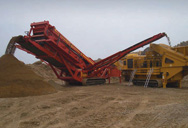
four principles of mill and ball ratio - mozart-loge …
Planetary Ball Mill. The mechanics of this mill are characterized by the rotational speed of the plate ωp, that of the container relative to the plate ωv, the mass of the charge, the size of the ball, the ball to powder ratio and the radius of the container. A schematic of the planetary ball mill is shown in Fig.2.4. Figure 2.5 shows a ...

Optimization of continuous ball mills used for …
The L/D ratio of the ball mill was varied in four steps of 1.75, 2.1, 2.79 and 3.49, and the ball charge filling ratio was varied in three steps of 15%, 20% and 25%. The experiments clearly indicated that the optimal L/D ratio and the optimal ball charge filling ratio are different for each feed fineness.

Ball mill - Wikipedia
Planetary ball mills are smaller than common ball mills and mainly used in laboratories for grinding sample material down to very small sizes. A planetary ball mill consists of at least one grinding jar which is arranged eccentrically on a so-called sun wheel. The direction of movement of the sun wheel is opposite to that of the grinding jars (ratio: 1:−2 or 1:−1). The grinding balls in the grinding jars are …

Ball Mills - an overview | ScienceDirect Topics
Oleg D. Neikov, in Handbook of Non-Ferrous Metal Powders, 2009. Tumbling Ball Mills. Tumbling ball mills or ball mills are most widely used in both wet and dry systems, in batch and continuous operations, and on a small and large scale.. Grinding elements in ball mills travel at different velocities. Therefore, collision force, direction and kinetic energy between two or more elements vary ...
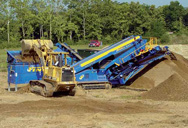
How should we select ball (size, grading) for …
Amount of milling balls is equal from 10:1 (balls:material) to 15:1. Whats size of ceramic powder particles? Ratio 1:1 is well for ball mill.

Ball Milling - an overview | ScienceDirect Topics
Ball milling and ultrasonication were used to reduce the particle size and distribution. During ball milling the weight (grams) ratio of balls-to-clay particles was 100:2.5 and the milling operation was run for 24 hours. The effect of different types of balls on particle size reduction and narrowing particle size distribution was studied. The milled particles were dispersed in xylene to disaggregate the clumps. …
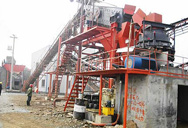
Ratio Balls In Vertical Ball Mill - plaidwebshop.nl
What Is Ratio Balls In Vertical Ball Mill. vertical mill vs ball mill Like all ball mills the speed and ball size have an effect on how the vertical ball mill works What Is Ratio Balls In Vertical Ball Mill [Chat Online] spec ex Defense Technical Information Center. of the ball the smallest theoretically possible can be referred to as critical For example on fig 1 for the dotted curve relating ...
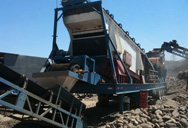
Effect of Ball to Powder Weight Ratio on the ...
-TiC nanocomposite powders were successfully synthesized with different ball to powder weight ratios (BPR) by ball milling of Mo, Si, Ti and graphite elemental powders. Formation of this composite was studied by X-ray diffraction (XRD). Morphology and microstructure of the milled powders were monitored by scanning and transmission electron microscopy (SEM and TEM), respectively. There was ...
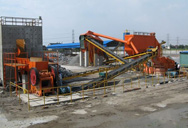
Planetary Ball Mill - 911Metallurgist
The mechanics of this mill are characterized by the rotational speed of the plate ωp, that of the container relative to the plate ωv, the mass of the charge, the size of the ball, the ball to powder ratio and the radius of the container. A schematic of the planetary ball mill is shown in Fig.2.4. Figure 2.5 shows a laboratory planetary mill.